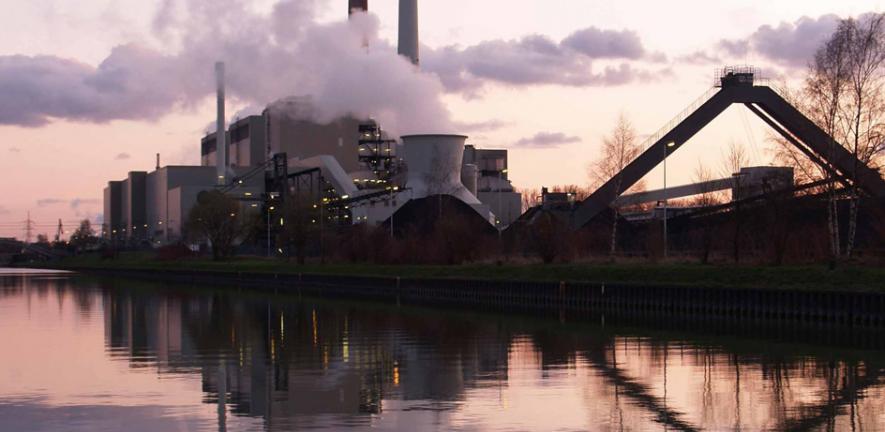
Coal – affordable and still abundant – but also the worst offender when it comes to fuel-associated carbon emissions. How well can coal be cleaned up?
Coal – affordable and still abundant – but also the worst offender when it comes to fuel-associated carbon emissions. How well can coal be cleaned up?
The hope is that techniques such as those being developed in Cambridge will facilitate cleaner and more efficient coal power generation in the future.
Coal generates the largest share of the world’s electricity and remains the most plentiful of all the fossil fuels. Figures released by the World Energy Council have estimated that reserves of economically recoverable coal are sufficient to last for another 150 years. Its abundance and low cost have ensured coal’s place as a mainstay of energy generation worldwide and especially in developing countries. However, burning coal produces more of the greenhouse gas CO2 than most other fossil fuels per unit of energy generated. How can our need for coal be balanced with a move towards a carbon-constrained future?
With funding from the Engineering and Physical Sciences Research Council (EPSRC), chemical engineer Dr John Dennis has teamed up with engineer Dr Stuart Scott to create a coal combustion process that not only maximises energy output but also captures pure CO2, which can then be sequestered in the Earth.
Clean coal technology
Coal power stations usually burn highly pulverised fuel, turning the hydrocarbons to CO2 and water (as steam, which drives turbines to generate electricity). Because the coal burns in air, which contains a large amount of nitrogen, the resulting CO2 is impossible to sequester without being purified first. Not only is this costly, but a coal-fired station might use as much as a third of its energy output just to run a carbon-capture plant.
The EPSRC-funded study has gone back to the drawing board to find a more effective way of removing CO2, focusing on improving the efficiency of a process for coal combustion known as chemical looping combustion (CLC). In conventional CLC, the fuel is first oxidised in a fuel reactor by a solid metal oxide (the oxygen carrier) in the absence of air, creating steam and pure CO2. When the steam is condensed, what’s left is almost pure CO2 plus the reduced metal. The metal is then regenerated into metal oxide in an oxygen reactor, generating substantial quantities of heat for power generation, and is recycled to begin a new cycle of reduction and oxidation.
However, using solid fuels in CLC is difficult because the particles of fuel and oxygen carrier cannot be easily separated. Drs Dennis and Scott are developing a technique that overcomes this by gasifying the fuel first (essentially turning coal into hydrogen and carbon monoxide). In the first phase of the cycle, solid fuel is fed continuously into a bed of oxygen carrier, through which is passed steam or CO2, or both: this gasifies the fuel, which reacts in turn with the carrier to form CO2 and steam. When the carrier becomes depleted towards the end of the first phase, the feed of coal is stopped and the inventory of carbon in the bed is allowed to gasify and combust until it is sufficiently small. In the second phase, air is passed through the bed, instead of steam or CO2, regenerating the depleted oxygen carrier. A new cycle then starts.
In a further modification of the process, the researchers have found that they can also isolate hydrogen by regenerating the oxygen carrier in the presence of steam. The resulting hydrogen is clean enough to be used in a fuel cell; the process also has the desirable outcome of exporting heat energy in addition to the hydrogen energy, and also produces pure CO2 that could be sequestered. Work is ongoing to develop synthetic calcium-based sorbents to capture the CO2 for sequestration.
The UK Government’s White Paper ‘Our Energy Future’ recognised the important part that coal-fired generation plays in widening the diversity of the energy mix ‘provided ways can be found materially to reduce its carbon emissions’. The hope is that techniques such as those being developed in Cambridge will facilitate cleaner and more efficient coal power generation in the future.
For more information, please contact Dr John Dennis (jsd3@cam.ac.uk) at the Department of Chemical Engineering and Biotechnology, and Dr Stuart Scott (sas37@eng.cam.ac.uk) at the Department of Engineering.
This work is licensed under a Creative Commons Licence. If you use this content on your site please link back to this page.